Darlly
High Flow Filtration Systems
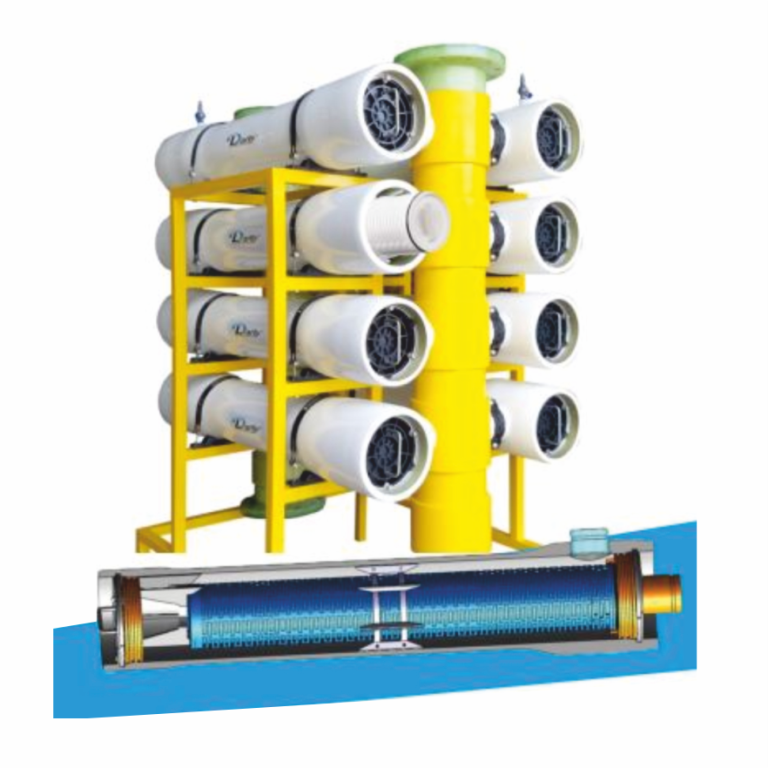
Applications
- Desalination Systems Municipal Water Industrial : SWRO & BWRO System Pre-filtration
- Water : Process Water / Wastewater & Reclaimed Waters
- Irrigation : Storage tanks for Landscaping Sprinklers
- Food & Beverage : Pre-filtration or Polishing Filtration
- Oil & Gas : Oil/Gas well Injection & Produced Water
- Chemicals & Petrochemicals Automobile Finishing Amine Sweetening
- Electronics Manufacturing Manufacturing of Ics, Memory Drives
FOR SUPERIOR FLOW RATES & LOADING CAPACITY
Dax Industries is associated with Darlly Filtration Systems China.
DarIIy High FIow fiItration system are styIed on the design of corrosion resistant FRP pressure vesseIs. These provide considerabIe reduction in capital investment versus stainless steeI construction and make use of a quick-acting closure. Each vesseI has the convenience of one filter element that can be exchanges in seconds.
High FIow fiIter eIements are avaiIabIe in both poIypropyIene and glass micro-fiber media in ratings of 0.5 to 100 microns, and in both nominaI and absoIute retention performance The unique layered construction provides exceIIent retention across a wide range of flow rates. Each six inch diameter 60″ length cartridge can handIe flow rates of up to 500gp, with the inside-to-outside flow path alIowing for high contaminant holding capacity. Superior flow and long filter life make Darlly High Flow fiIters an ideal choice for a wide variety of critical process filtration applications.
The innovation of advanced German pleating technology allows the filter elements to offer higher surface area resulting in superior flow and media utilization. With a tapered pore structure and fine fiber denier, the result is better dirt holding capacity,
low resistance to flow, superior filter performance and overall better value for the user.
The inside-to-outside flow configuration and core-Iess construction of the DarIIy High FIow fiIter eIement alIows it to be tightIy compacted to minimize disposal costs. Maintenance requirements and production downtime is dramaticaIIy reduced in comparison with conventionaI depth fiIters . Service personaI wiII find it easy & convenient remove used eIements since alI solid contamination is trapped inside of the filter cavity.